Tank Internals Demystified
Well, it’s a mystery, and it isn’t. When we get into rebed projects and open up the tank, we find all sorts of distributor designs. There’s a wide variety and they all have their pros and cons – and the OEM who built the system generally considers their design proprietary. Internal distribution systems are integral to a wide variety of water treatment applications: filtration, softening, and deionization. In many cases, the performance of an existing system can be improved by upgrading the distribution system if the vessel design permits.
In reality, there’s a lot of science that goes into engineering these, which is why we ask so many questions when a replacement is needed. For industrial applications, distribution systems (at least the better ones) take into account flow rate; pressure drop; number, size, orientation, and spacing of the holes in the laterals and whether or how they are screened. This can vary with the size of the pressure vessel as well. The goal is to provide uniform flow through the media/resin bed and avoid channeling.
In small-diameter fiberglass tanks, we frequently see a basket-type strainer for the distribution system since FRP tanks usually don’t have a manway to install them. These may be installed at the end of a riser pipe or screwed into the tank head.
The Inverted “H” design relies on directing the service and rinse flows off the upper tank head for distribution of flow. This is the lowest-cost design and is typically seen in smaller, commercial-grade systems. The downside of this design is that it is a poor collector of backwash flow.
The hub-radial design consists of a center hub with radial laterals (similar to a bicycle wheel). These provide good flow distribution and backwash water collection in vessels 60” in diameter and smaller; the cost is moderate. However, above 60” in diameter, the ends of the laterals are too far apart to provide uniform flow.
The header-lateral design consists of a center header with laterals that reach the tank's sidewall. These provide the best flow distribution and backwash collection however are the highest cost design, typically 15-20% higher than the hub-radial style.
For some applications, a header with dropped laterals is used, which consists of a center header with laterals extending to the bottom of the dished head. This utilizes the volume of media in the bottom head, but particles can become trapped and not effectively backwashed out.
In older systems, we sometimes see strainers embedded in concrete in the bottom head or the false bottom of the vessel, so there is no need for a gravel support bed. However, the strainers can become plugged over time or broken – and replacing them can be a huge undertaking!
To determine whether your system performance could be improved by an internal distribution upgrade, contact your Process Solutions, Inc. sales representative!
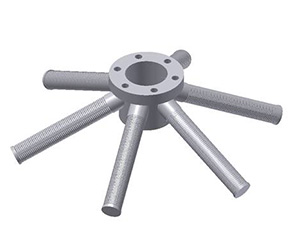
Hub-Radial Distributor Design
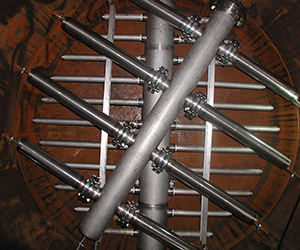
Header-Lateral Underdrain